
Revolutionizing Shop Floor Management: AI-Driven Automation with iDataOps
February 12, 2025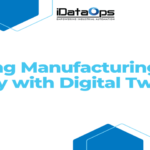
How Digital Twins and IoT Integration Are Enhancing Predictive Analytics for Manufacturing Efficiency
March 17, 2025How Machine Learning Models Are Powering Predictive Analytics for Smart Factory Operations
The future of manufacturing is here, and it’s smarter than ever. As industries adopt digital technologies, machine learning (ML) and predictive analytics are driving a new era of efficiency, agility, and innovation on the factory floor. By predicting potential issues before they even arise, manufacturers can take proactive steps to ensure their operations run smoothly and efficiently. In this blog, we’ll dive into how machine learning models are enhancing smart factory operations and how tools like manufacturing production management software are helping manufacturers leverage the power of predictive analytics.
Why Predictive Analytics Matters in Smart Factories
Predictive analytics uses historical data and real-time inputs to forecast potential issues, such as equipment failures, production delays, or quality control concerns. In a smart factory, these forecasts provide manufacturers with valuable foresight, helping them address challenges before they disrupt the production process.
For instance, manufacturing production management software gathers critical production data and feeds it into machine learning models. With integrated solutions, manufacturers can combine data from both Operational Technology (OT) and Information Technology (IT) systems, allowing for a more holistic view of factory performance. This approach ensures that manufacturers can predict and respond to issues before they escalate.
How Machine Learning Boosts Factory Efficiency
1. Proactive Maintenance: The End of Unexpected Downtime
Downtime is one of the most expensive and disruptive challenges in manufacturing. Thanks to predictive analytics powered by machine learning, manufacturers can now foresee potential machine failures and address them before they cause a halt in production.
By using manufacturing production management software, manufacturers can monitor equipment in real time. By integrating data from machines, sensors, and IoT devices, they gain comprehensive insights into equipment health, allowing for proactive maintenance scheduling. This minimizes downtime and ensures smooth production.
2. Unlocking the Full Potential of Equipment with OEE Tracking
Overall Equipment Effectiveness (OEE) is a key metric for measuring the efficiency of manufacturing equipment. Machine learning can provide deeper insights into OEE by identifying underperforming assets and uncovering inefficiencies in the production process.
Integrating OEE tracking software with machine learning enables manufacturers to optimize equipment usage and improve productivity. Real-time data analysis helps to enhance overall equipment effectiveness by targeting areas where performance can be improved.
3. Better Product Quality with Predictive Insights
Quality control is a top priority for manufacturers, but maintaining consistent product quality can be challenging. Predictive analytics helps manufacturers catch potential quality issues early by analyzing real-time data and historical trends.
By using integrated data systems, manufacturers can monitor production data in real time and identify any deviations from quality standards before they affect large batches. This enables quick corrective actions, ensuring that only high-quality products are delivered to customers and reducing waste in the process.
4. Streamlining Production with Predictive Scheduling
Effective production scheduling is crucial to maintaining an efficient factory floor. Machine learning can optimize production schedules by analyzing data to predict demand, allocate resources efficiently, and reduce bottlenecks.
By integrating predictive analytics into the scheduling process, manufacturers can streamline their production operations. Real-time tracking of raw material usage, machine performance, and production volumes helps ensure smoother and more efficient production cycles.
How Software Systems Fuel Predictive Analytics in Smart Factories
To fully realize the benefits of predictive analytics, manufacturers need robust software solutions that can collect, manage, and analyze data across the factory floor. Manufacturing production management software plays a critical role in this by providing real-time data on every aspect of the production process.
By combining OT and IT data, manufacturers gain a comprehensive view of their operations. This unified approach allows for smarter decision-making and better insights into every stage of the production process.
Key Benefits of Machine Learning in Smart Factories
-
Increased Operational Efficiency: Predictive analytics helps manufacturers identify inefficiencies early, streamline operations, and reduce downtime.
-
Cost Reduction: With proactive maintenance and optimized production schedules, manufacturers can cut costs associated with unplanned downtime and maintenance.
-
Enhanced Product Quality: By leveraging real-time insights, manufacturers can ensure higher-quality products and minimize defects.
-
Better Decision-Making: Integrated solutions provide manufacturers with a unified, data-driven approach to decision-making, improving productivity and driving continuous improvement.
Conclusion: The Future of Smart Factory Operations
Machine learning and predictive analytics are transforming the manufacturing industry, enabling businesses to operate more efficiently and reduce costly disruptions. By integrating manufacturing production management software into their processes, manufacturers can unlock powerful insights that drive continuous improvement.
With predictive analytics, manufacturers can anticipate issues, optimize resources, and keep production lines running at peak performance, ensuring they remain competitive in a fast-paced market. These technologies offer a future where manufacturing operations are not just reactive, but intelligently proactive.
In the ever-evolving landscape of smart manufacturing, having a comprehensive, data-driven solution is crucial. iDataOps empowers manufacturers by integrating Operational Technology (OT) and Information Technology (IT) systems, enabling real-time data management and predictive analytics. By offering unparalleled visibility into operations, iDataOps helps manufacturers optimize production efficiency, reduce downtime, and enhance overall productivity.
With advanced features like unified data integration, real-time insights, and predictive maintenance capabilities, iDataOps is helping companies harness the power of machine learning to streamline operations and drive continuous improvements in the manufacturing process.