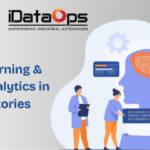
How Machine Learning Models Are Powering Predictive Analytics for Smart Factory Operations
March 3, 2025
From Big Data to Smart Data: How Industry 4.0 is Shaping Data Intelligence Platforms for Manufacturing
April 7, 2025How Digital Twins and IoT Integration Are Enhancing Predictive Analytics for Manufacturing Efficiency
In today’s fast-evolving manufacturing landscape, Digital Twins and IoT integration are transforming how manufacturers optimize production processes. These technologies of manufacturing production management software, combined with predictive analytics, are not only improving operational efficiency but also revolutionizing maintenance strategies, minimizing downtime, and boosting overall productivity.
If you’re looking to stay ahead of the curve, understanding how Digital Twins and IoT can enhance manufacturing operations is essential. Let’s dive into how these technologies are reshaping the future of manufacturing efficiency.
What Are Digital Twins in Manufacturing?
A Digital Twin is a virtual replica of a physical asset, such as machinery or an entire production line. This dynamic digital model simulates the behavior of its real-world counterpart, enabling manufacturers to monitor performance and predict issues before they escalate.
When paired with IoT sensors, which capture data in real time, Digital Twins become an invaluable tool for manufacturers. These virtual models receive continuous updates from the physical systems, offering insights that allow for better decision-making and optimized workflows.
The Power of IoT in Predictive Analytics
IoT (Internet of Things) devices are embedded in machines, equipment, and production lines, collecting real-time data. When this data is integrated into predictive analytics, manufacturers can anticipate issues before they disrupt production.
For example, machine downtime tracking software can help detect subtle warning signs such as temperature shifts or unusual vibrations. By analyzing this data through predictive models, manufacturers can take proactive steps to prevent breakdowns and reduce costly downtime.
This powerful combination of IoT and Digital Twins enables manufacturers to make smarter, data-driven decisions, ensuring production runs at optimal levels.
How Manufacturing Production Management Software Supports Efficiency
Integrating manufacturing production management software with Digital Twins and IoT further enhances operational efficiency. These software solutions act as centralized platforms that help manufacturers track and manage every aspect of their production process.
By connecting production monitoring software with real-time data from Digital Twins, manufacturers can monitor machine performance, track production metrics, and even optimize inventory management. This integrated approach ensures that manufacturers can respond to changing demands quickly and efficiently.
Additionally, having data from multiple sources, including OEE tracking software, allows manufacturers to gain deep insights into overall equipment effectiveness. With this information at their fingertips, decision-makers can fine-tune operations to reduce waste and improve output quality.
Reducing Downtime with Predictive Maintenance
One of the most valuable outcomes of combining IoT, Digital Twins, and predictive analytics is the ability to reduce downtime. With machine downtime tracking software, manufacturers can track the health of their equipment in real time, gaining insights that can predict when maintenance is required.
Instead of waiting for machines to fail, manufacturers can use predictive models to schedule maintenance during planned downtime, avoiding unexpected disruptions. This proactive approach extends the lifespan of equipment, reduces repair costs, and ensures consistent production performance.
The Future of Manufacturing Efficiency
By leveraging Digital Twins, IoT, and manufacturing production management software, manufacturers can stay ahead of the competition and unlock new levels of operational efficiency. With predictive analytics, manufacturers can optimize workflows, improve maintenance strategies, and significantly reduce unplanned downtime.
As these technologies evolve, the future of manufacturing will be even more interconnected, data-driven, and automated, driving higher productivity and lower operational costs across the industry.
Conclusion: Embracing the Power of Digital Twins and IoT for a Smarter Manufacturing Future
Integrating Digital Twins and IoT with predictive analytics offers manufacturers a unique opportunity to optimize their operations. It also enhances productivity and minimize disruptions. With the ability to monitor machine health, predict failures, and streamline workflows, the combination of these technologies is reshaping the manufacturing landscape.
Manufacturers who embrace these innovations will be well-positioned for success in an increasingly competitive and data-driven world.